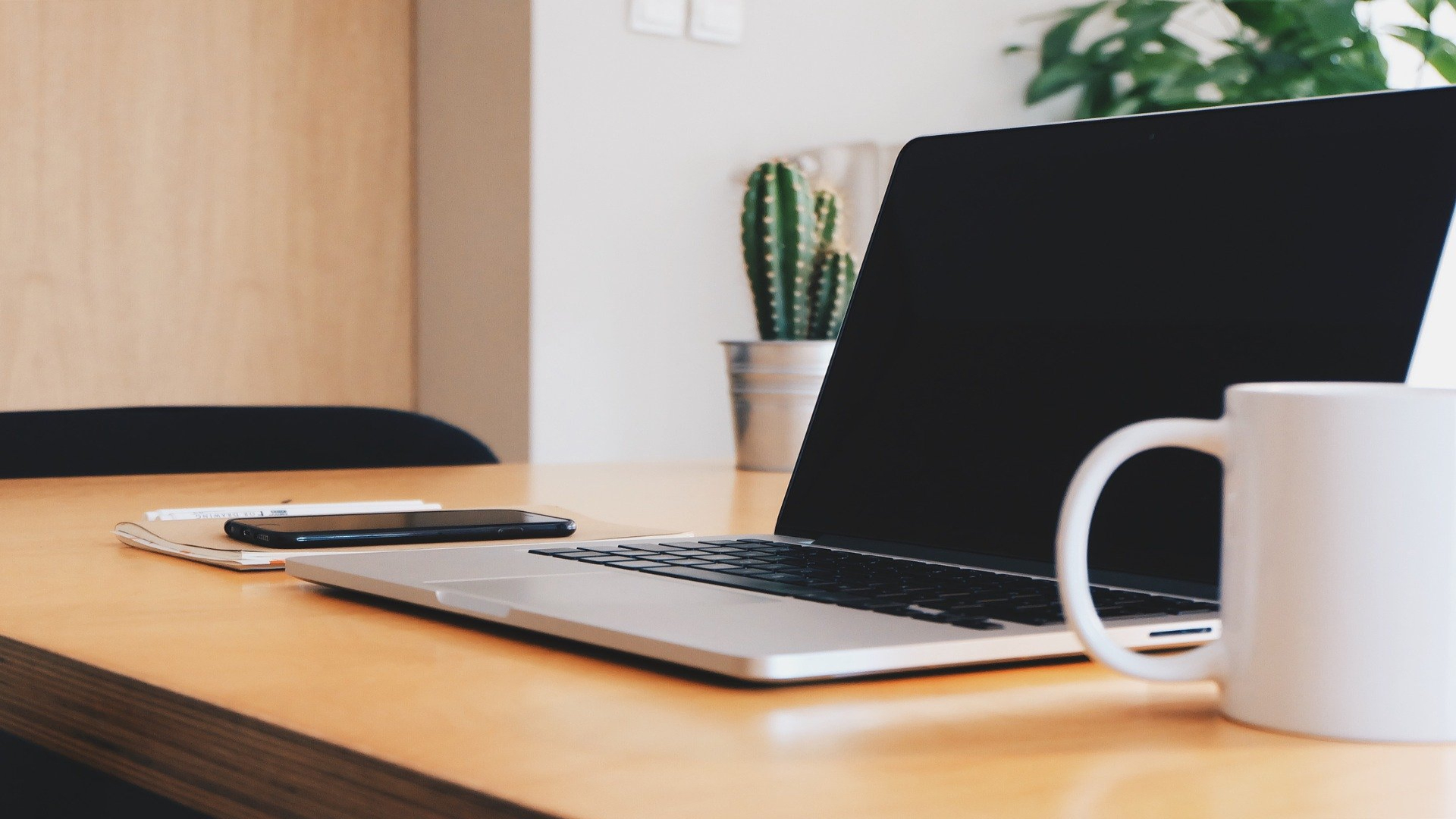
Keep your employees safe: Implement a workplace safety program
As a business leader, you might wonder how to implement or improve the safety program at your organization. This is especially true for small business owners and managers who might question if the time and effort to develop a safety program is worth it.
Regardless of the size of your company, a workplace safety program is always worth it!
An effective workplace safety program serves as a set of defined practices intended to prevent accidents, reduce costs, and engage employees.
In this article, we will explore:
- Why you need a workplace safety program
- The basics of a workplace safety program
- Resources that you can turn to for help
A workplace injury can cause major disruptions.
Every year, millions of people in the United States sustain a serious work-related injury or illness. The foremost issue is the untold personal impact that an injury can cause. Individuals and families can suffer greatly from an injury sustained on the job. Injured employees must seek treatment and may miss significant time from work while recovering.
Likewise, a company can face higher workers’ compensation premiums, medical expenses, legal fees, replacement worker training, and lost productivity.
A workplace injury can have a devastating impact, but many see a safety program as just a formality. But it’s more than that—a safety program that meets your company’s needs and satisfies regulations is good for business and will keep your employees safe.
Here are five essential steps to implementing a workplace safety program.
According to OSHA, you should start small and build from there:
“You can begin with a basic program, set simple goals, and grow from there. If you focus on achieving goals, monitoring performance, and evaluating outcomes, your workplace can progress to higher levels of safety and health achievement.”
Let’s take a closer look at five critical elements of an effective safety plan.
1) Get management buy-in. Think about it: executives implement the vision for the entire company. From sales goals to budget approvals, all employees look to the top for guidance. Company leaders must signal their commitment to safety. A top-down approach sets the proper expectations.
A clear written policy can help company leaders establish their commitment to safety. It allows the company to communicate that workplace safety is an everyday goal and just as important as sales and productivity. You want to establish a work culture where safety is a requirement, not an afterthought.
2) Engage your employees. Program participation is key. Without employee engagement and a shared understanding, even the most in-depth safety plan won’t work.
How do you encourage employees to engage with and follow a safety plan? Refer to step 1 above! It all starts at the top. Employees are more likely to participate and practice safety at work if company management expresses their commitment to safety and leads by example.
You should also know that engagement is an ongoing process. Here are a few suggestions:
- Provide employees with safety resources, such as training, on a regular basis.
- Make it known that employees can give honest feedback.
- Give positive reinforcement to employees that actively participate.
- Involve employees in every aspect of the program.
- Sit down and formulate safety policies with those on the front line.
When employees feel that their input is welcome, they are far more likely to engage and practice good safety habits.
3) Identify hazards and assess solutions. Failure to identify hazards is a major problem and the cause of many workplace injuries. Be proactive rather than reactive and identify hazards before they cause harm.
Collect and organize new information directly from employees. For example, you might know that the company purchased new equipment. Ask your team questions like: is there a safety manual in place? Is there an emergency procedure in place? Do they have the proper personal protective equipment (PPE) required to operate the equipment?
Many hazards are not obvious and may not be included in your current safety plan. Be sure to review safety plans often and update or revise as needed. Note that you can get very in-depth when performing a safety assessment—and you should, especially if your safety program is outdated. OSHA provides many relevant resources to help you conduct a safety review.
4) Provide education and training. Managers, employees, and stakeholders must know the safety program and understand procedures. This knowledge empowers workers to practice safe habits. Training also helps refine policies to increase safety across the board.
Effective training consists of:
- Peer-to-peer training
- On-site training
- Worksite demonstrations
Training should focus on program education, emergency plans, safety goals, and hazard identification procedures.
5) Monitor performance. Once you have a safety program in place, you will want to take a step back and monitor performance.
Start by defining key progress indicators. Be sure to track the total number of injuries on the job. Write a full report of each incident that you can refer to at any time.
Define rules that allow you to track key factors, including employee participation, hazard identification, and timeliness of corrective actions after you identify a hazard.
Whenever possible, monitor performance with indicators that you can measure. Collecting and analyzing data makes it easier to get the full picture. Refer to the OSHA guidelines for more information.
Implementing a workplace safety program can seem challenging, but there are plenty of resources to help you get started.
There are many online resources that can help you implement a safety program. You should first turn to OSHA, the federal agency in charge of occupational safety. OSHA offers comprehensive, step-by-step guidelines detailing how to implement a safety program.
OSHA – Quick Links:
- Safety checklist
- Training and educational resources
- Policy implementation procedures
- Federal laws and regulations
OSHA also offers in-person safety consultations, a no-cost program for small- and medium-sized companies. You can find additional resources at your state’s occupational safety board. For example, companies in California can use Cal/OSHA’s website for guides and information about laws that apply to California businesses. You can also turn to professional employer organizations that work with companies to develop health and safety programs. These organizations may be a good fit for your company if you do not have a dedicated HR department or if you need outside guidance.
Companies that create a culture of safety can expect better outcomes when it comes to employee satisfaction and overall productivity. Take the time to review your existing safety plan. Work with others to identify areas that require improvement. Use online and in-person resources, like those available via OSHA, to set your company on a path toward greater work safety and improved employee health.
Start a conversation with a Bay Alarm security expert.
Related Articles
Agricultural businesses face a variety of security concerns. They have to protect livestock, expensive machinery, and... Read More >
Preventing theft and inventory shrinkage is crucial for retail and grocery stores already challenged by razor-thin... Read More >
Security guard services offer on-the-ground protection for businesses seeking an additional layer of safety for their... Read More >
The Phoenix metropolitan area continues to experience incredible population growth. With year-round sun, affordable housing, and... Read More >
Office buildings pose a variety of security challenges that businesses must address to safeguard their people,... Read More >
Retail theft is one of the leading causes of business owners’ stress and economic hardships. In... Read More >
Outdoor and remote locations can push traditional surveillance systems to their limits. Fixed systems face challenges... Read More >
From the early 20th century, Los Angeles has been known across the world for its unparalleled... Read More >
Commercial earthquake preparedness is critically important, especially in a city like San Francisco with its long... Read More >
Hospitals face many security challenges, one of which is ensuring proper storage and monitoring of controlled... Read More >
It’s common to think of cybersecurity and physical security as two separate operations. However, in the... Read More >
If you live in California, you are no stranger to the challenges of getting insurance. It’s... Read More >
Fire safety is a priority everywhere, but in California it’s especially urgent. To be prepared, business... Read More >
Protecting educational campuses and facilities is an increasingly urgent and complicated problem. Campus buildings can be... Read More >
Is it time to update your business’s security system, but you’re unsure where to start? We... Read More >
Managing properties, whether one or multiple, means constantly juggling challenges. Dealing with buildings in different cities... Read More >
As security technology advances, so do the options for customizing security protocols. A security protocol tells... Read More >
Live video monitoring is a next-generation security service that combines new technologies in threat detection (way... Read More >
Businesses and people are now using facial recognition technology to make payments, bank online, and as... Read More >
In their research report on “The Future of Physical Security,” execs from Microsoft and Accenture interviewed... Read More >
Customer: Laborers Training School Laborers Training School provides construction-based labor training to union workers in multiple locations... Read More >
As we mentioned in a previous article, several trends in the security market have made live... Read More >
News about artificial intelligence is everywhere these days. So it’s no surprise that business owners are... Read More >
The best runners in the world aren’t simply fast; they’re efficient. The most popular cars don’t... Read More >
What are security GUARD services? Security agent services (SAS) are live security guards who work on... Read More >
A typical customer in 2023 wants—and expects—a shopping experience that works for them. A challenge for... Read More >
There’s no denying that AI-powered technology offers you a chance to step up your business’s security... Read More >
You’ve probably heard of behavioral analytics. It’s everywhere these days, shaping our world and dramatically influencing... Read More >
Understanding who is at your business—and when—is a key priority for most business owners. Another obvious,... Read More >
Video security has come a long way, so much so that the full capabilities of a... Read More >
What is live video monitoring? Live video monitoring is a commercial security service that deters crime... Read More >
According to Security Magazine, more than 2,000 first-responder agencies across the US currently use drones and... Read More >
Scaling a business is an exciting time filled with new possibilities. But it can also bring... Read More >
If you’re relatively handy and feel like you have a solid understanding of technology, you might... Read More >
A video security system is only effective if it’s installed properly. The most advanced, AI-based camera... Read More >
Preserving employee safety can be a big challenge when expanding your business to multiple locations. As... Read More >
According to the National Insurance Crime Bureau, more than one million cars were stolen across the... Read More >
Has a speeding car in the next lane ever distracted you from seeing a pothole until... Read More >
Every business owner deals with risk: it’s part of doing business. Some risks are worth taking,... Read More >
An unsafe work environment poses hazards for businesses beyond the physical risks to employees. It can... Read More >
The best modern business security systems feature some of the most advanced technology on the planet.... Read More >
Build a culture of safety the right way Protecting employees and the office work space takes... Read More >
Warehouses are complex environments that present many potential hazards to employees. According to the Occupational Safety... Read More >
Protect Your Business Without Breaking the Bank Protecting staff, inventory, and physical property is a priority... Read More >
Security tools work best when they fit the exact needs―and capacity―of your business and staff. The... Read More >
Implementing an effective security system for your business isn’t as simple as installing a camera, setting... Read More >
Following business safety regulations isn’t a choice but an obligation. Ignoring compliance standards not only puts... Read More >
Business leaders know how difficult choosing a security system can be. Every organization has specific needs... Read More >
One of the most frequent reasons business owners approach security companies is, unfortunately, one of the... Read More >
Keeping up with trends and technological advancements in the security industry can be challenging. Knowing where... Read More >
Robbery, theft, and arson cost US businesses over $17.2 billion in losses in 2021. As a... Read More >
Searching for a smoke alarm system for your business? You’re probably going to need a smoke... Read More >
Do you know what it takes to stay compliant with building fire codes? Not every business... Read More >
Picture walking from your office building to your car at the end of the day. Others... Read More >
How do you keep up with evolving fire codes for your property? Amid everyday business concerns,... Read More >
Several high-profile fires have raised the urgency of fire protection for cannabis facilities. So, what is... Read More >
If you’re searching for the right video surveillance system, you have likely run across the network... Read More >
Waste is kindling for fires. If you work in the waste industry, you are likely aware... Read More >
The numbers don’t lie. Despite all the focus on cybersecurity, cybercriminals remain a costly threat to... Read More >
School security is important from kindergarten through college. Prioritizing safety can put students and staff at... Read More >
Companies of all industries depend on warehouses to store and ship valuable goods. And storing large... Read More >
As the business owner or manager of a retail store, you need to be aware of... Read More >
Video content analysis (VCA), also known as video analytics, is a video surveillance technology used to improve the response to crime and other emergen Read More >
Protecting your business and staff during the holidays can be challenging, especially with all the surrounding... Read More >
Access control systems give business owners and managers the power to control what areas employees and... Read More >
One big reason Bay Alarm is different from other security system companies: it’s locally operated and... Read More >
California voters made recreational cannabis legal in 2016. Since then, thousands of cannabis dispensaries and other cannabis-related businesses... Read More >
The answer is yes, 3G is going away. The network will no longer exist at the end... Read More >
Habitat for Humanity is building a first-of-its-kind 3D-printed home in Tempe, Arizona, as part of their... Read More >
In 2020, owners of some multifamily residences in San Diego began receiving notices titled “Retroactive Residential... Read More >
Here’s some reality TV you probably haven’t seen: actual property crimes in progress, captured by Bay... Read More >
An important part of managing your business is ensuring the safety and security of your employees,... Read More >
Open Supervised Device Protocol (OSDP) is an access control systems standard developed by the Security Industry... Read More >
Contact sensors are security devices typically installed on doors and windows. They can notify you and... Read More >
Selecting the right type of security camera for your home or business is critical, as security... Read More >
Standard commercial security guard services include agent response, guard patrol, and standing guard, all of which... Read More >
Biometric security systems digitally identify people through biological signatures, like fingerprints, facial recognition, and eye scans.... Read More >
Ever try scheduling service appointments for multiple locations with a big security company? Chances are, you... Read More >
Having a basic knowledge of burglar alarm systems will help you decide what kind of system... Read More >
Like all security technology, security cameras have come a long way in recent years. As people... Read More >
Your fire alarm and sprinkler systems must satisfy all federal, state, and local regulations. If it... Read More >
Believe it or not, commercial security cameras used to give us blurry images. Luckily, those days... Read More >
Are you hesitant to get a security and fire alarm system for your business due to... Read More >
Fire alarm systems keep buildings and building occupants safe from fires. While it is easy to... Read More >
Catalytic converter theft has become a big issue for car lots as the price of materials... Read More >
An IP camera, or internet protocol camera, is a type of digital security camera that receives... Read More >
When shopping for a business security camera system, you might have the option to choose a... Read More >
Despite advanced security technology, false alarms do happen. Non-emergency events are major strains on local emergency... Read More >
Video alarm verification pairs your security system with an alarm monitoring center. In the event an... Read More >
A motion sensor, or motion detector, is an electronic device that uses a sensor to detect... Read More >
A fire alarm system is one of the most important security features of any building—they are... Read More >
Traditional metal keys can be easily lost, locks must be professionally re-keyed if an ex-employee fails... Read More >
How do you change an employee’s code on your business DMP system? It’s easy! You... Read More >
The ‘Users’ page allows you to manage all of the users on your system. Connect to... Read More >
Schedules and profiles work together to let you customize how and when you give an individual... Read More >
Modern security camera systems are great for monitoring your home or business, as many systems offer... Read More >
The ‘System Overview’ page gives you quick access to the parts of your system you interact... Read More >
For those looking to increase the safety of their home or business, it can be tempting... Read More >
The history page on VirtualKeypad.com allows you to view the most recent events on your system.... Read More >
As a small business owner, you need more than just a security camera or burglar alarm.... Read More >
The reports page allows you to generate reports about what’s been happening on your system. You... Read More >
Holiday dates allow you to adjust your system schedules on special occasions throughout the year. Once... Read More >
The Virtual Keypad website allows you to conveniently manage your access control system using your computer... Read More >
The Bay Alarm Link mobile app makes arming and disarming your business security system easy. Take... Read More >
Adding users to your Business DMP system is easy, and only takes a few steps. To... Read More >
Constructing a new commercial building—be it a retail space, apartment complex, skyscraper, or sporting arena—is a... Read More >
Bay Alarm’s BayGuard+ live video monitoring puts you in complete control of your business’s security system.... Read More >
There are a wide variety of home and business security devices and systems. You can opt... Read More >
Your home or business burglar alarm system increases the safety of everyone and everything within. It’s... Read More >
In 2016, there were over 11,000 reported construction-site equipment thefts in the United States, which accounted... Read More >
A cyber security breach, or data breach, is an intentional or unintentional release of private information... Read More >
The coronavirus pandemic (COVID-19) is shifting most day-to-day work operations from the office to the home.... Read More >
The California State Fire Marshal recently announced that it is still essential for contractors to ensure... Read More >
Fire is one of the top risks to any small business. According to the National Fire Prevention... Read More >
While you can’t always predict supply and demand, ensuring the protection of your business is one... Read More >